8月8日,我国第二艘国产大型邮轮正式在中国船舶集团有限公司旗下上海外高桥造船有限公司开工建造。这标志着中国船舶工业已初步掌握大型邮轮设计建造关键核心技术,在开启“双轮戏珠”新时代的同时,向大型邮轮批量化、系列化建造迈出了具有里程碑意义的一步。

大型邮轮与航空母舰、大型液化天然气(LNG)运输船被誉为造船领域“皇冠上的明珠”,而大型邮轮也是中国造船业至今尚未摘取的最后一颗“明珠”。大型邮轮代表了一个国家的装备建造能力和综合科技水平,全力推进大型邮轮设计建造是中国船舶工业转型升级、提升中国制造在全球影响力的标志性工程。
更大、更绿色
今天开工建造的第二艘国产大型邮轮在同型首制船的基础上进行了一系列优化。该船总吨位约14.2万吨,总长341米,型宽37.2米,设计吃水8.17米,最大吃水8.4米,最高航速22.7节,拥有客房2144间。相比于首制船,第二艘大型邮轮总吨位增加了0.67万吨,总长加长了14.4米,客房数量增加了19间。同时,根据《国际海上人命安全公约》(SOLAS)2020破舱稳性要求和国际海事组织(IMO)Tier III 标准&船舶能效设计指数(EEDI)第二阶段要求,新增了2套脱硫塔和选择性催化还原(SCR)系统,这也使第二艘国产大型邮轮将在未来成为一座更为绿色环保的“移动海上城市”。
值得一提的是,相比于首制船,第二艘国产大型邮轮在外观上也做了一些修改,其顶部的烟囱造型从“丸子头”改为“大背头”。同时,第二艘大型邮轮还配置了高达16层的庞大上层建筑生活娱乐区域,设有大型演艺中心、大型餐厅、特色餐馆、酒吧、咖啡馆、购物广场、艺术走廊、儿童中心、SPA、水上乐园等丰富的休闲娱乐设施,可满足乘客更为丰富的生活和娱乐需求。
据了解,2018年11月,我国首制国产大型邮轮建造合同正式签署。目前,首制船建造已全面进入关键的内装和系统完工调试的“深水区”,工程进展有序可控。而在中国船舶集团的统筹指挥以及项目合作伙伴嘉年华集团和芬坎蒂尼集团的大力支持下,外高桥造船通过引进消化和自主创新,相继开展邮轮设计、建造、项目管理等专项攻关,形成了一系列科技创新成果,这也为外高桥造船继续坚持开放合作、实现共赢发展开创了路径,也为第二艘国产大型邮轮建造奠定了基础。
有经验、更有信心
为了实施和推进国产大型邮轮工程,外高桥造船在中国船舶集团领导下,统筹各方资源和力量完成了一批大型邮轮船厂适应性改造工程。特别是打造了薄板生产智能车间,以MES系统为核心,搭配工业互联网技术,实现了产线智能化管控,不仅提升了分段建造效率和精度管理水平,还构建了邮轮产品系列化建造能力。
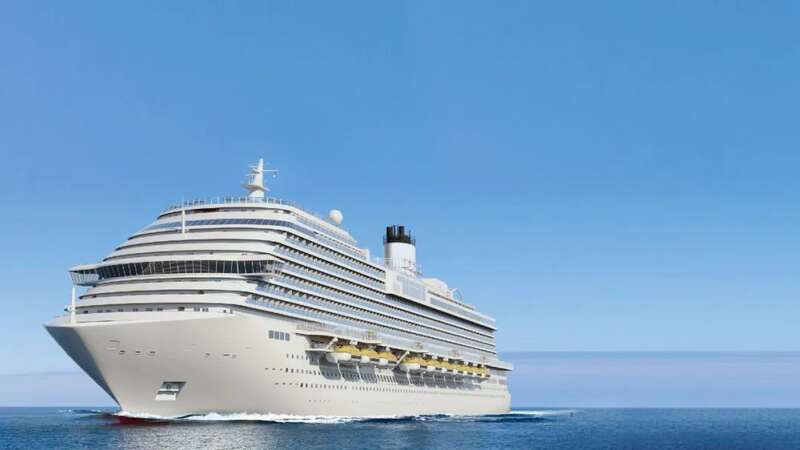
与此同时,外高桥造船还开发并运用了新一代造船管理平台SWS TIME,实现了设计、采购、现场管理全过程信息化协同管控;通过研发一体化移动应用平台,加速协同协作效率,实现了“人找数据到数据找人”的模式转变。在此基础上,外高桥造船还组织行业内优势单位开展技术集智攻关,攻克了邮轮重量控制、安全返港、动力系统、综合电网、舱室环境、振动噪声等关键设计技术。
此外,外高桥造船还跨行业、跨地区寻源吸纳了超过500家全球供应商推进邮轮设计建造任务,尤其是在邮轮内装领域,与来自美国、意大利的54家服务商建立了合作。更为重要的是,外高桥造船还开创性地将陆地酒店工程领域长期积累的技术、施工和管理能力引入邮轮内装工程领域,深度开展三维设计软件的二次开发,实现了船舶行业三维软件与建筑行业BIM技术的深度融合应用。
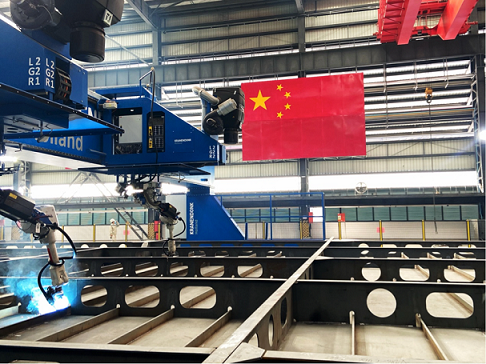
第二艘国产大型邮轮相较首制船的设计建造周期被压缩了整整6个月,且船型和配置的新变化也需要外高桥造船针对安全返港设计、重量控制、防火设计等进行重新开发论证。得益于首制船建造积累的对外合作和自主创新等经验,外高桥造船将继续加大科技创新投入,深度赋能邮轮工程,进一步完善项目管理,通过质量、安全、成本、周期等风险管控,全力推进第二艘国产大型邮轮建造任务。
据了解,目前,第二艘国产大型邮轮详细设计已完成约40%,生产设计模型平衡和结构生产设计发图工作已全面启动。在建造方面,外高桥造船正从工艺工法创新、设备调试以及人才队伍建设等方面不断强化生产准备。